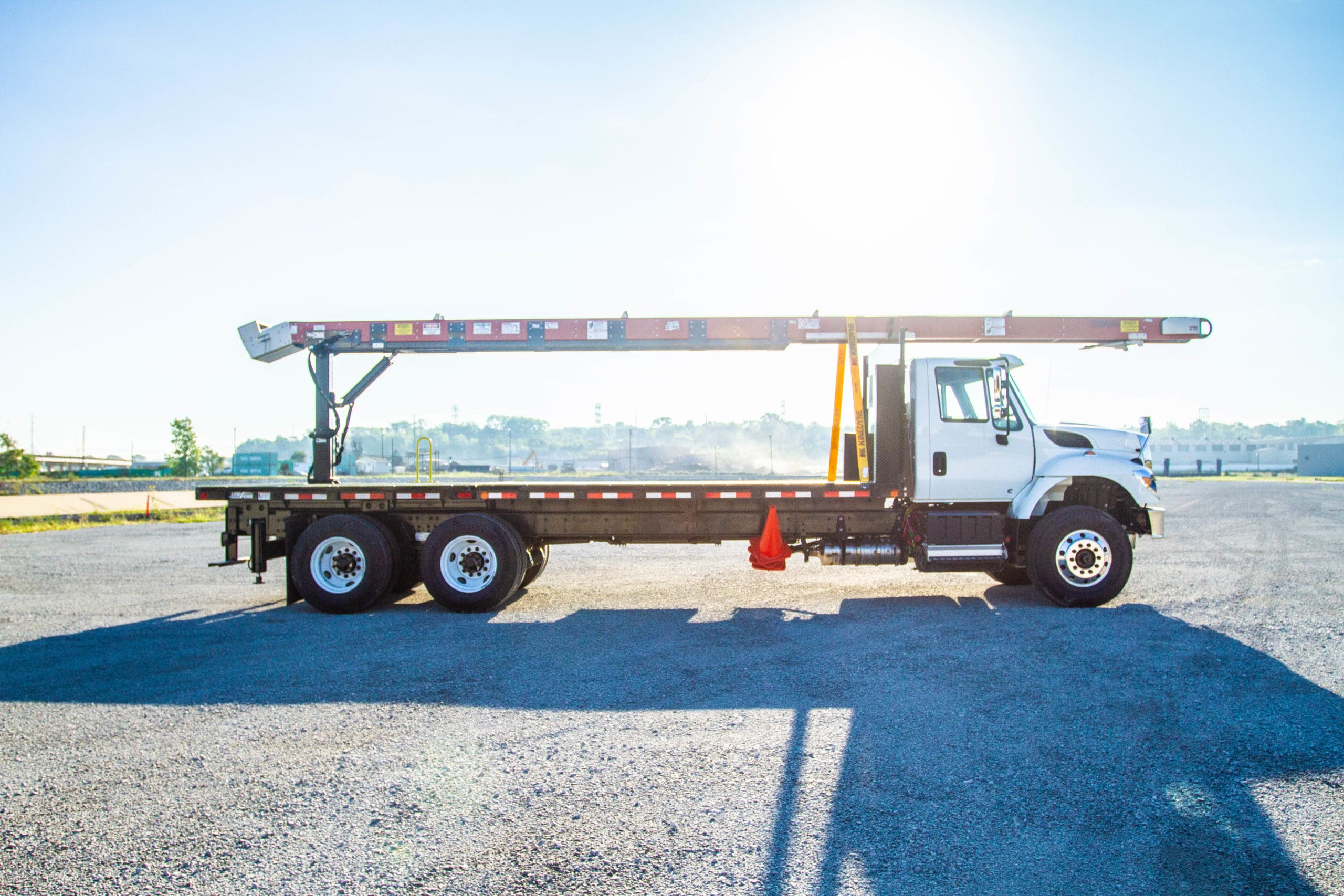
Roofs and roofing practices have changed a lot over the years, evolving to include more cost-friendly and environmentally friendly options. The roofing industry has long since transitioned from days spent tediously cutting, measuring, and loading roofing materials.
Now, people can call up local companies and have a new roof installed in mere days using proper equipment. For more information on the roofing industry and how equipment has changed over the years, keep reading!
Evolution of Roofing
The history of roofing began thousands of years ago. Roofs provide shelter and protection from weather and animals. They can also help provide insulation and keep temperatures comfortable year-round.
Roofs were once very raw and constructed solely by whatever types of materials were readily available. Some of the earliest roofs used materials such as animal skins, clay, or rocks. Wood was also sometimes used, but it could sometimes rot and attract pests.
Clay Tile
One can find clay tile on roofs as far back as 10,000 B.C. Clay tile quickly spread from Asia through Europe. The Roman and Greek empire used clay tiles for most of their buildings, and this continued even up until the early periods of America.
While you can still fine clay tile roofs to this day, they are slightly different from their predecessors.
Wood Roofs
Wooden roofs were often used in Colonial America since wood was widely available. While it is still a common type of roofing today, it has better features that make it less susceptible to rot, pests, and more.
Wooden roofs in the early days were more prone to widespread fires. Most of these wooden roofs were completely handmade.
People chopped down and cut up trees. When transporting heavy logs, wheelbarrows or other simple modes of transportation were often incorporated.
Thatched Roofing
Thatched roofing was fairly common for nomadic tribes. It was easy to construct for temporary living conditions. Usually, water reeds were used for this type of roofing.
Yet, some people used other materials like wheat or long straw. Thatched roofing didn’t last long since it was not very durable. It was soon replaced with stone and other methods.
The benefit of thatched roofing was that it is more fire-resistant and easier to install. However, in extreme weather, these roofs were more likely to collapse. Like wooden roofs, most thatched roofs were constructed by hand with limitations in equipment.
New Roofing Materials
Present-day roofing has come a long way and includes durable materials and techniques that withstand harsh weather. Some of the modern materials one can pick for a new roof include:
- Asphalt composite shingles
- Metal roofing or shingles
- Wood shingles or shakes
- Clay tile
- Slate shingles
These new materials and types of roofs have allowed some homeowners to keep their roofs for up to 100 years. Slate shingles are known to last someone’s entire life, although they can be a bit more expensive upfront.
Many modern homes have asphalt composite shingles, which can still last up to 20 or 30 years. Replacing them has also become easier with the invention of new equipment.
Green roofs have risen almost 10% during recent years and are becoming more popular options in heavily populated cities with flat roofs. These unique types of roofs incorporate gardens and vegetation on top of the roof, which can help reduce rooftop and air temperatures.
New Roofing Equipment
In the early days, roofing was constructed by hand and required manual transportation of heavy materials. Not only was this extremely time-consuming, but it also put a lot of workers at risk.
Some of the frequently used equipment by roofers are:
- Pry bars/shingle removers
- Retractable knives
- Retractable tape measures
- Hammers
- Hammer staplers
- Dump trucks
- Roofing hatchets
- Fall equipment
- Roofing conveyors
Roofing conveyors are pieces of equipment that have helped the roofing industry tremendously. This modern equipment allows the seamless transition of materials from the truck to the roof.
Boom trucks and forklifts also assist with constructing a new roof. Boom trucks are frequently used for lifting or transporting heavy materials and can either be used in conjunction with roofing conveyors or independently.
Not only does this make roofers more efficient and productive, but it also puts them at less of a risk for injury, since the machine is doing the bulk of the transport work.
Construction and roofing trucks (new, used, or for rent) are critical in easing the process of bringing in new materials and disposing of older materials. The benefit of construction trucks is that they can improve the efficiency of construction.
Technology and Roofs
Advancements in technology have primarily driven the rise in modernized equipment for roofing. In earlier years, roofers cut and measured everything by hand, using hand saws and hammers.
While that is still true, to a degree, new pieces of equipment have made construction much more efficient. Materials have shifted over the years and have become more fire-resistant and resistant to harsh weather.
Nowadays, there are sealants, software, automatic tools, inspections, and other uses of technology that have driven advancements in the durability of roofs.
For getting roofing done in a productive manner, you need the right specialized truck. For any construction needs, contact us today for new or used heavy equipment.